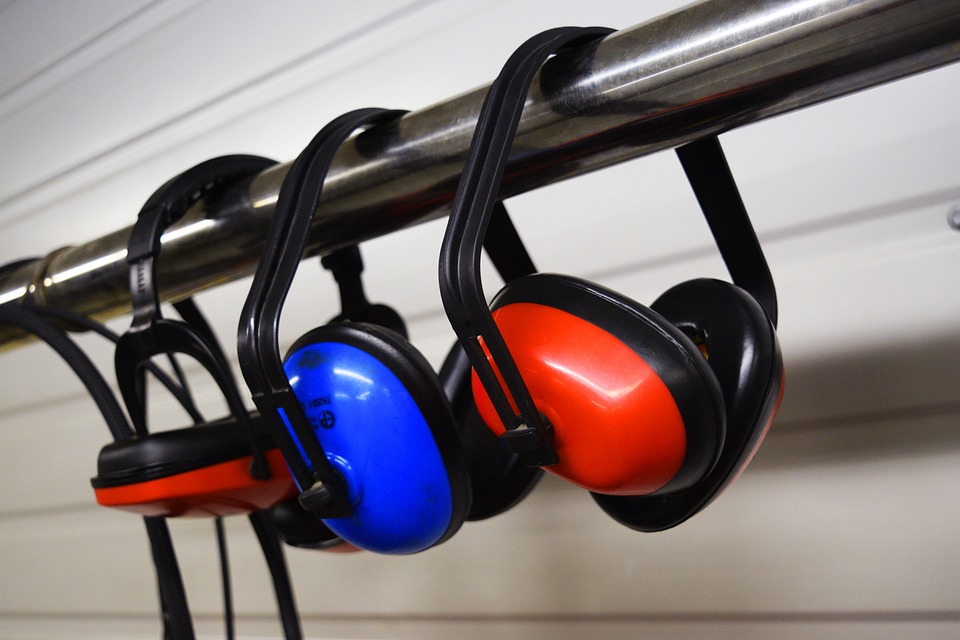
Adhering to ear protection standards in the workplace means following regulations 7 (hearing protection), 8 (Maintenance and use of equipment) and 10 (Information, instruction and training) of the Control of Noise Regulations at Work Regulations 2005.
The law was passed in order to establish a variety of exposure limits which set out the average level of noise an employee could be exposed to during a working day. Loosely, the law set out what ear protection would be needed and, by extension, what extent of damage is acceptable and not acceptable. Every workplace in Europe must now adhere to this system, including providing safety equipment when the average level is exceeded.
The Details of the Control of Noise Regulations at Work Regulations 2005
The act introduced exposure limits that are set at decibels (dB). Each dB is given a rating that corresponds to its exposure. Employers must provide hearing protection and specific hearing protection zones at 85 decibels, plus they must officially review and assess the safety of their staff at 80 decibels. The absolute exposure limit is 87 decibels, which takes into account the protection of safety equipment.
What Is Ear Protection: Signposting and Safety Equipment
Ear protection signs are a visual reminder to employees to put on safety equipment. Ear protection includes ear plugs, ear defenders, headphones, and ear muffs. Signs must be placed up well in advance of encountering the noise and should be in a clear, easy-to-spot place.
Fundamentally, though, employers are expected to replace dangerously loud machines with quieter, more modern counterparts as a long-term solution. While this isn’t always feasible, it is the best way to deal with damage to employee hearing.
What is “Ear Protection Must Be Worn” Sign Meaning
As with all safety signs, these ear protection signs must comply with the harmonised standard EN 7010 and the Signs and Safety Regulations 1996 law. These govern the correct use of the symbol or pictogram, as well as colour and layout.
The “Ear Protection Must Be Worn” sign is blue and white, complete with a pictogram of a face with ear protection on.
Other Uses for Ear Protection
Ear protection can also help protect against dust, water, and foreign objects entering the eardrums. This is especially important in workplaces that have air polluted with heavy elements or whenever hazardous chemicals are handled in large amounts.
Claims Against Employers
Last year, a successful industrial deafness claim was filed by former violist Chris Goldscheider against the Royal Opera House. The musician suffered a life-changing hearing injury in 2012 which managed to be the basis for the first claim of acoustic shock in legal records.
Goldscheider was incorrectly seated directly in front of the brass section of the where he endured noise levels that exceeded 130 decibels without any protection. For comparison’s sake, 130 decibels is roughly that of a jet engine.
Want to Learn More?
Stay up to date with the world of health and safety and ear protection with Label Source’s range of ear protection signs. In addition, follow us on Facebook and Twitter to keep up with the latest health and safety news.