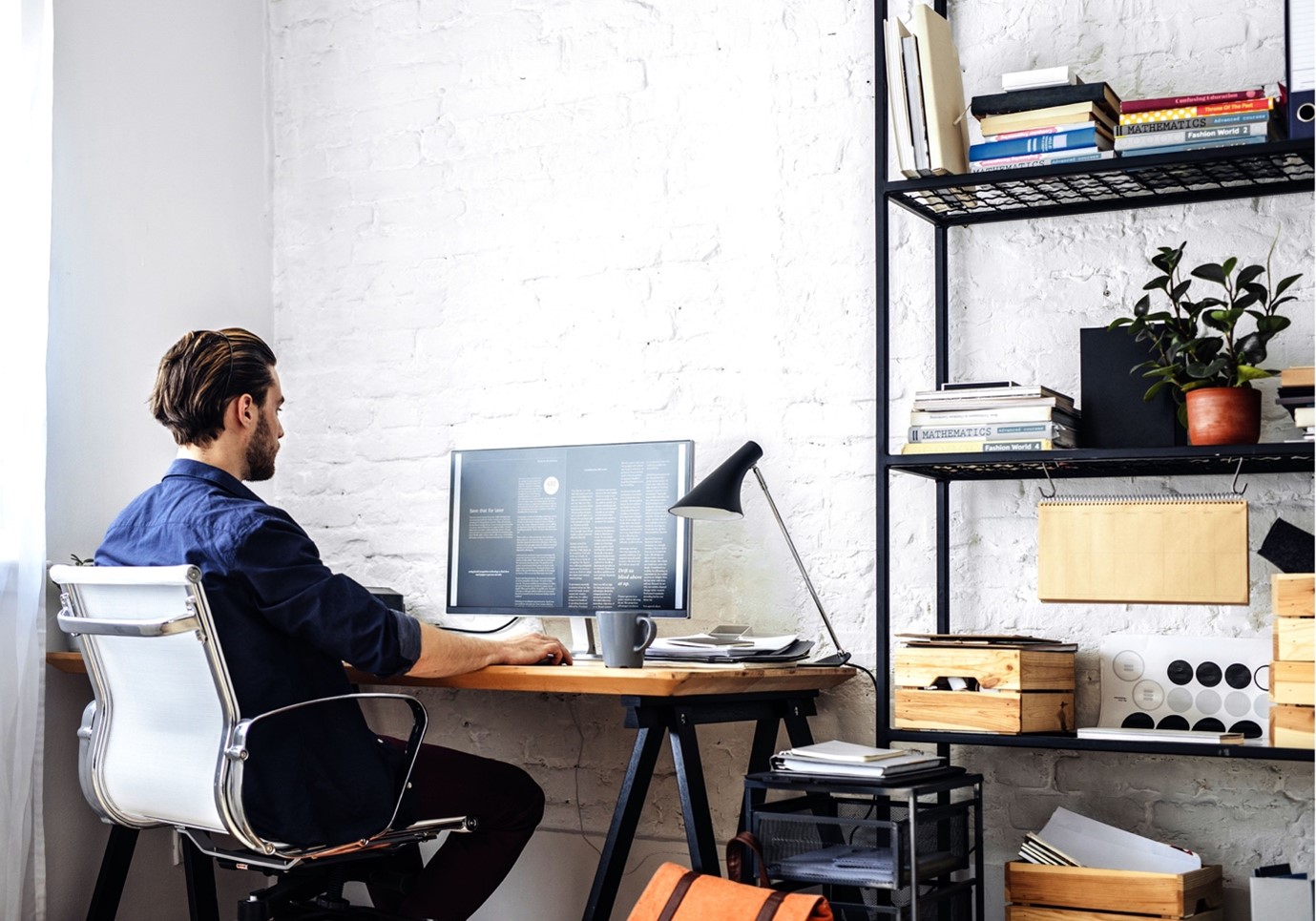
An employer’s responsibilities don’t end when an employee leaves the premises. Nothing has made this fact more evident than the coronavirus pandemic, which has seen swathes of the working population quickly switch to working from home.
Employers quickly realised their responsibilities for their staff didn’t begin and end in the office. Several issues came to the fore, namely:
- How can employers manage workplace stress outside of the office?
- How can they manage workloads?
- How can they ensure ergonomic best practice is followed?
- Is their current health and safety procedure still suitable?
Thankfully, a number of working from home guidelines were available to follow from the HSE and the Government. While for many we’re in the final stretch of working from home, the precedent of the last few months is set to change working behaviour for others. Continuing to stay at home for the long-term is certainly an option for some.
To ensure you’re keeping your employees safe going forward, discover how much responsibility an employer has for their staff when they are working from home.
What are the Working From Home Guidelines?
Legally, employers must ensure the health, safety and wellbeing of their employees, even at home.
Individual guidance varies depending on the workplace, but the majority of work from home guidelines can apply to any industry.
Namely, the most important sections of the working from home guidelines are as follows:
- Ask employees to carry out their own risk assessments and relay back any issues. This sounds larger than it is – it’s essentially ensuring employees have a comfortable working environment.
- Respond to this risk assessment information to the best of your ability.
- Stay abreast of government guidance.
- Make reasonable adjustments for disabled employees.
- Regularly keep in touch with employees to manage mental health and make any reasonable adjustments for those who are struggling.
Just because employees are at home doesn’t mean they’re free of risk or an employer’s responsibility.
Health & Safety: Managing Stress and Mental Health at Home
Most modern workplaces should have mental health procedures already in place, but this may not be sufficient for at-home working.
An increase in workload, worries around the current coronavirus response and disconnection from peers can understandably lead to an increase in stress and, therefore, an impact on mental health.
Employers must be proactive when it comes to this issue. Procedures should be put in place to recognise signs of stress early and to act on them.
Ultimately, the best health and safety policy when it comes to mental health is to be flexible. This should include:
- Supporting a flexible work/life balance.
- Mimicking in-office social events and check-ins. Maintaining company culture can have positive knock-on effects.
- Creating action plans for workers who are suffering with their mental health.
- Encouraging employees to turn to additional support should they need it.
DSE Equipment and At-Home Ergonomics
An employer should provide the equipment needed for an employee to work from home. This can be everything from IT equipment to desk chairs to headsets – essentially, anything your staff had in the office should be provided for at-home work.
This applies to workplace ergonomics, too. An employer must provide ergonomically safe Display Screen Equipment (DSE) such as keyboards and mice to prevent long-term injuries from poor posture, eye fatigue or muscle degradation.
To complement this, employers should encourage employees to create a comfortable working environment and take time for regular breaks, exercise and light.
Read more about ergonomics with our in-depth blog: Labels and Ergonomics: Using General Signs To Improve Performance.
Prepare for a Return to Work With our Safety Signs
Overall, by listening to workers, following risk assessments and giving them the equipment they need, you are fulfilling your responsibility to workers at home.
The transition to working from home won’t end with coronavirus, so prepare for these policies to be used in the long-term.
However, plans are already being put in place across the country to return to the office, too, so you need to be ready for any eventuality.
To prepare for a return to the office, be sure to check out our range of safety signs. We also have a selection of social distancing signs for those returning to the office in bubbles.