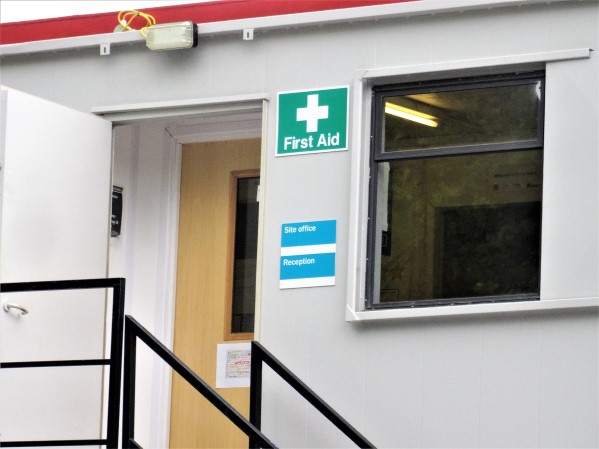
Some things last a long time. Believe it or not, the first aid sign, which is recognisable all over the world, is over 900 years old.
The sign has been accommodated, modernised and used by different entities countless times over. It is the oldest sign we use in modern life and is, in some ways, a testament to how a well-made sign can stand the test of time.
Below, we discuss the history of the first aid sign and why it is has remained so important.
A History of First Aid
When you think of a first aid sign, you commonly think of its red-and-white variant. However, for most of its history, the sign was green and white, which is sometimes still used today.
The classic green-and-white logo comes from the sign’s origins: the Hospitallers of St. Lazarus. This group, which existed around 1119, was founded by crusaders as a military order in a leper hospital in Jerusalem. While this group was eventually used as a military force later in the twelfth century, it was originally a group of hospitallers made recognisable by their distinct green-and-white cross crest.
The order prevailed through the medieval period, receiving protection from King Philip IV of France and eventually working closely with the Roman Catholic Church. While originally being interwoven with leper treatment, the order pivoted to maintaining proper birth conditions well into the 1800s.
While the order became embroiled and eventually dissolved in the fallout of the French Revolution, its green-and-white cross became synonymous with health.
The cross, in red form, was adopted by the Geneva Convention in 1864 as an inversion of the Swiss flag. As wars raged on, the first aid symbol eventually became synonymous with “don’t shoot!” and to signpost the safety of medics and nurses on the frontline.
Both forms now coexist – the red cross is synonymous with the aptly named Red Cross humanitarian charity and the green is used to signpost first-aid-related entities.
The Importance of First Aid and its Sign
Under The Health and Safety (First Aid) Regulations 1981, it is the legal requirement of the employer to enable first aid to occur should someone fall ill at work.
As part of these regulations, a first aid box and an appointed officer should be on-site at all times. A first aid box must be adequately signposted in case of emergency, so an appropriate use of a first aid sign is also legally required.
In essence, a workplace should have an appropriate sign and equipment to direct workers when an accident occurs. Panic can quickly set in, which makes signs and labels that much more essential.
Research in 2018 showed that only 5% of adults have the confidence and skills to act in an emergency. Labels may seem small, but having something objective to hold onto in these moments can be the difference between acting calmly and losing confidence.
First Aid Signs From Label Source
We stock a range of first aid signs in various shapes, sizes and designs. No matter where you work, we’ll have something for you.