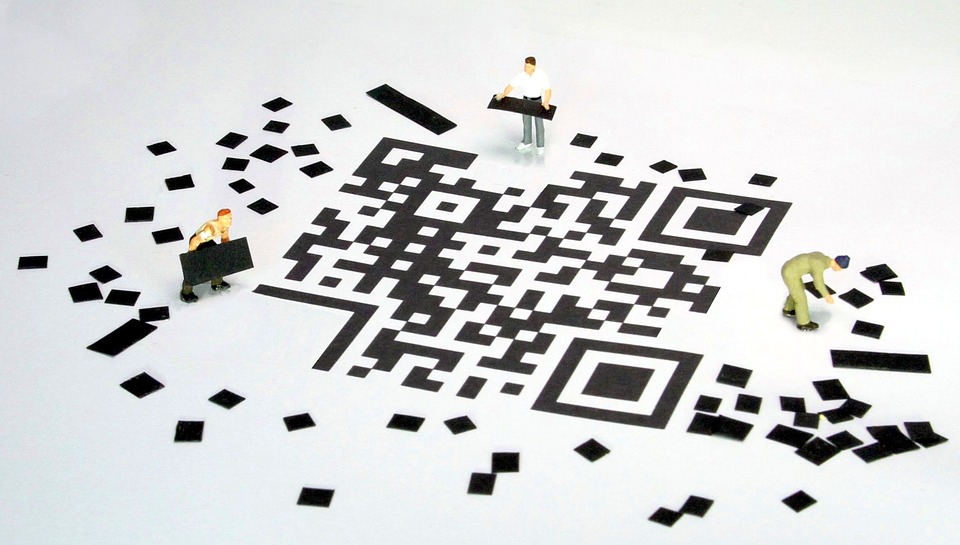
QR codes, an abbreviation for quick response codes, have become integral to modern communications, customer services and even marketing since its inception in 1994.
Originally, the QR code was created by the Japanese automotive industry to track vehicles during the manufacturing process.
Soon after, the code’s ability for high-speed component tracking allowed it to catch on in broader industries, before becoming a symbol of modern communications. Nowadays, QR codes can be purchased and even printed at home.
However, figuring out how to print QR codes on labels can be difficult, so check out our process below.
What Is A QR Code And How Does It Work?
A QR code can look a little random at first, but its intuitive design allows for machines to read code quickly. In real terms, it allows for quick communication of sensitive and detailed information. The code can be read by any smartphone or specific electronic devices, allowing for communication links to texts, emails, websites, phone numbers and everything in between.
Marketing companies can use the code on posters and websites for access to specific, secret websites or a concert ticket could be scanned by security to ensure its viability. Wherever there’s communications or a need to verify information, QR codes can be used.
How does it work, though? In layman’s terms, the QR design is essentially an image hyperlink that can be used offline. A URL, phone number or ticket number can be encoded, plus information relating to which format the information should be opened in.
QR codes began as a niche commodity in the West but took off in a big way in Japan and the East near its inception. Nowadays, Western businesses are catching on making the code a common sight on billboards, posters, tickets, magazines, websites, etc. If you want to link people to something while in the offline world, a QR code is the way to go.
How To Print QR Codes On Labels
Given the information above, it’s easy to think printing QR codes would be a difficult, technical process. However, figuring out how to print QR codes on paper is as easy as printing barcodes – it’s a simple process, but getting the steps right is essential.
First, you’ll need to generate your QR code. This can be achieved through a number of QR code generators online. Simply place your link or information in the appropriate section, then the website will produce a QR code like magic.
When downloading a QR code, there’s usually scope for some form of customisation. You can edit the QR code to your desired brand colours or design, ensuring it seamlessly embeds itself into your label’s design.
Then, simply paste the QR code onto a printable document via Word or other software. There are a few best practices to follow here, namely ensuring your QR code is placed in an area that is easy to read and scan.
Making sure it’s scannable is the most important point; not everybody has a good quality camera on their smartphone, so make sure even the oldest brick can take a clear picture of it. If your label has a tendency to curve too, then factor this into placement – you don’t want to effectively cut the QR code in half!
If you’re unsure whether the consumer base you’re producing labels for knows what a QR code is, then include some short instructions that answers “what is a QR code” and how to scan it. You may want to test the QR code before printing too to make sure there’s no technical niggles or miscommunication.
Finally, print the design on some good quality, applicable label or sticker paper.
Get Your Hands on High-Quality Labels
If that all sounds like too much work, Label Source has stocked the best in asset management barcode labels for a variety of uses. For more from the ever-changing world of labels, be sure to follow Label Source on Facebook and Twitter.