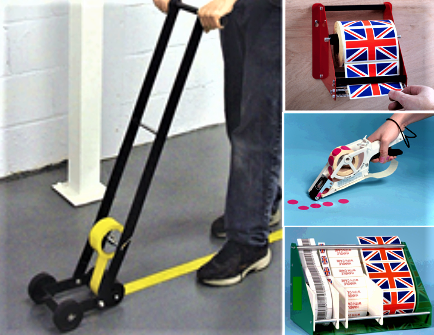
Marking floors and items is made easy with a tape applicator and dispenser, but its efficiency, effectiveness and safe use rely on a person using it properly.
Lots of places of work rely on the correct marking of floors and items to keep things running. Factories, for example, rely on properly marked flaws to help manage forklift traffic and the organisation of employees.
With just a few rolls of tape, a disorganised factory floor can become an inch-perfect workplace optimised for safety and efficiency.
Below, we discuss the uses of automatic tape dispensers, as well as how to use a tape applicator properly.
What is a tape dispenser called?
There are several different types of tape dispensers, so they can also often come under different names. A handheld tape dispenser, for example, may also be referred to as a tape gun or tape applicator.
How do I set up a floor tape dispenser?
To use a floor tape applicator, you must first apply self-adhesive floor tape to the sticker dispenser. Make sure it is placed properly before then using the tape on sealed floor surfaces. Never use the applicator on floors which are not sealed as this will lead to tape that is poorly affixed to the floor.
Essentially, floor tape applicators should be used on warehouse floors, aisles, clean corridors and assembly and sports halls.
Following the placement of the tape to the dispenser, simply press down on the handle and walk slowly and steadily in a straight line to ensure the tape sticks to the floor and remains neat.
How do you set up a handheld tape dispenser?
To set up a handheld tape dispenser, insert a new roll of tape into the tape dispenser after taking the old one out. Pull a few inches of tape off the end or the roll, then thread it through the roller and teeth until the tape is pulled taut.
All that’s left to do is simply push the tape onto the wheel of the dispenser, with the sticky side facing down.
Why use a tape gun?
If you know how to set up a tape gun (or how to load a tape dispenser), you’ll likely find that it has many more uses than you originally expected. Any time you need to quickly apply tape, your tape dispenser will be there to help you out.
Floor Markings with a Tape Gun
Businesses use tape applicators for a number of reasons, but the major motivation for businesses applying lines and stickers over their floors is to streamline and organise the workplace. For some businesses, it is essential to maximising efficiencies.
If places like factories had no floor organisation, they would be akin to chaos. Floor markings are a cost-effective option to shore up the long-term maintenance of walking traffic, as well as segregate two lanes of traffic for vehicles.
Floor markings can also synergise with safety symbols, meaning they can be an essential tool in workplaces having effective safety protocols.
Processing and Packaging
Once you know how to load a tape gun, whether handheld, floor-marking or otherwise, a tape gun can be used to seal boxes, package items, make quick repairs and more.
Find Your New Tape Applicator Today
Considering a tape applicator? Then browse the range of tape applicators and dispensers here at Label Source.