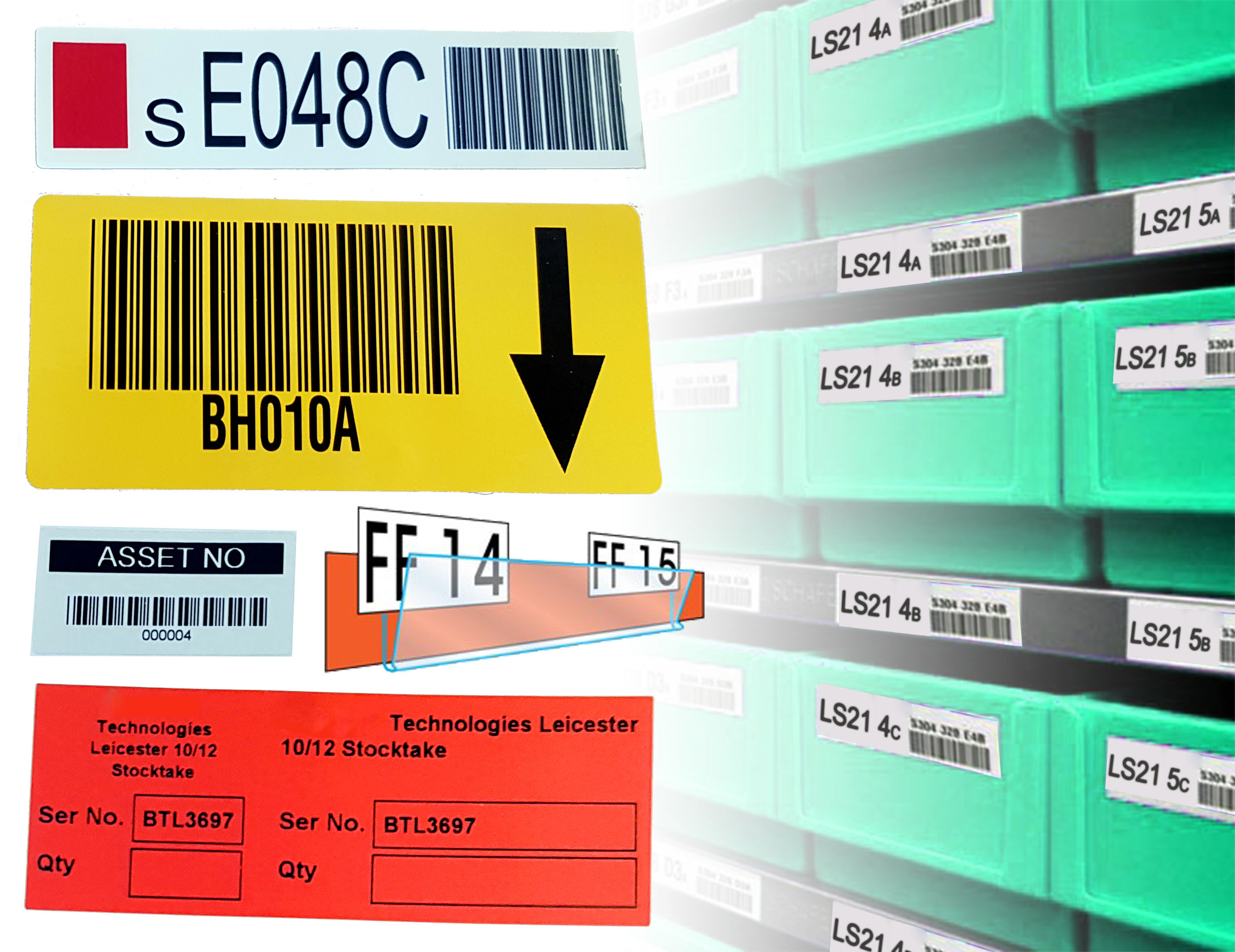
Serial numbers dictate much of modern stock control and distribution. They're an efficient method of communication, even though most see them as a bunch of random letters and numbers. The major advantage of a serial number is that it will always be unique, so there is little chance for confusion to occur.
However, given their unique nature, serial numbers can be complicated. When serial number labels are used by a business, there needs to be an understanding of how they function.
Below, we provide a full guide on how to use serial numbers, what serial numbers mean, as well as a short history of them.
What Do Serial Numbers Mean?
Much like fingerprints, each serial number is wholly unique. Serial numbers can be used everywhere, from hardware and software to banknotes and secure documentation.
A serial number provides an identity to a singular item or product. While some non-serial codes can identify a line or range of products, a serial number is reserved for one item only.
For a product range, a serial number will always begin with the item code for that number. So, if a business sold an item that had the item number “QX3000”, all serial numbers would begin with “QX3000”. The numbers after that would identify the specific product.
A stand-out example is with car manufacturers. Each car part has its own serial number, which helps with finding replacements, but also helps to trace the parts if the car is stolen.
By using serial numbers, a person or system can easily identify what the model is and the exact product in question. This can help a business organise stock, recalls and refunds effectively, as well as opening up avenues for automation.
When Were Serial Numbers Invented?
They seem like a modern invention, but the practice of numbering goods and property can be traced back to Roman times. Archaeological digs have revealed stonework from the Roman era that was inscribed with a basic set of serial numbers, so we’ve been numbering things for a long time!
Since then, humans have used serialised numbers to mark everything, mainly since they worked across different language and cultural barriers. As international banks and markets were founded, the need to have a system to regulate mass numbers of cash made serial numbers even more important. Following banks, export networks demanded a recognisable tracking system worldwide.
Serial numbers are now typically found on serial number labels and tags. Whether it’s a small business or an international conglomerate, businesses and institutions rely on serial numbers to function.
How to Use Serial Numbers Effectively
To use serial numbers effectively, you need two things:
- A system or database that records serial number data.
- Serial number labels.
The former is significantly more complicated than the latter. In essence, you need a stock control system that incorporates serial numbers. These are usually updated via scanners during import, export and recalls.
For serial number labels, you need to put a process in place wherein each product has a unique serial number. These are usually scanned or recorded at key stages from importing to exporting.
While some products have etched-in serial numbers, others use a label. These can be complemented by a barcode, which helps with tracking.
To learn more about the history and use of barcode labels, read our detailed blog on the subject: ‘How Did People Shop Before Barcodes? The History & Development of Barcode Labels’.
Without labels, it can be difficult to know what the serial number of a product is and can lead to disorganised stock control.
Get Your High-Quality Serial Number Labels Today
At Label Source, we stock a wide range of high-quality, self-adhesive serial number labels and tags.
If your business can benefit from the stock control serial numbers allows, then browse our full range of stock control labels today.