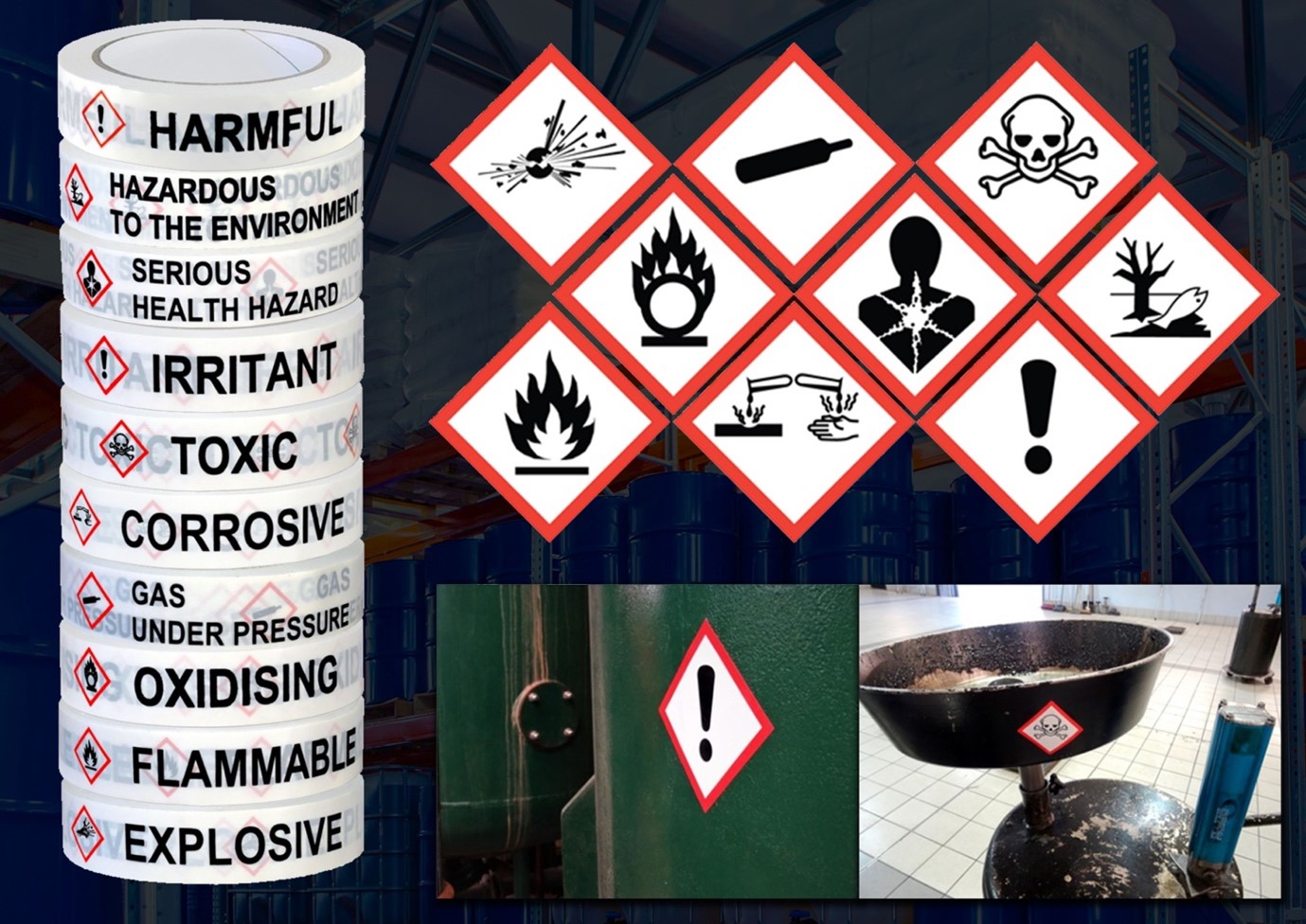
The Globally Harmonized System (GHS) is an agreed-upon set of rules managed by the United Nations. The system has several objectives:
- Classifying all health, environmental and chemical hazards.
- Ensuring presented information falls within international standards.
- Ensuring this system remains the same across UN nations.
However, as you can imagine, putting together such a comprehensive system across borders with separate laws, industries and cultures pose a challenge.
Below, we’ll breakdown what GHS labels are, as well explain its recent history.
What are GHS Labels?
GHS labels are simply labels which fall in line with the GHS’s requirements. They provide a brief overview of the hazard, how to deal with it and the steps to take afterwards.
We’ve discussed this in-depth with our blog: What Is A GHS Label and Why Is It Used?
When was GHS Introduced?
The Globally Harmonized System was officially introduced in 2003. However, this was the result of a long battle to get such a system introduced, which began in Rio in 1992.
In 1992, the Brazilian city hosted an event called the Earth Summit. There, the International Labour Organisation (ILO) – responsible for setting international labour standards – and the Organisation for Economic Co-operation and Development (OECD) – responsible for stimulating world trade - collaborated.
By taking aboard the concerns from multiple international governments and key stakeholders, they were able to put the foundation in place to create a “globally harmonized hazard classification and compatible labelling system”. The motivation for this was two-fold:
- To improve international safety standards.
- To remove safety hurdles in trade.
The aim was to get the system up and running by 2000, but organisers ran into issues and the need for expansion. In 1999, the GHS system was incorporated into the Committee of Experts on Transport of Dangerous Goods.
2002 saw the creation of an implementation plan after much back-and-forth. Then, after review, implementation was ready for 2003.
Since then, modernisation of GHS has occurred in line with new standards and requirements from the market; it essentially exists as a living document, usually iterated upon every two years.
What was the Impact of GHS?
The GHS had a number of immediate benefits, including:
- Improving the consistency of information supplied to employees.
- Providing the first international standardised approach to chemicals, hazards and data.
- Making the use of datasheets to log accidents and risks the standard.
- Enabling workers to understand signs and labels across cultural and language barriers.
Underpinning this was a greater awareness of personal safety around chemicals and other hazards, which naturally weaved into the improvement we’ve seen in health and safety standards since the millennium.
Explore GHS-Approved Labels Today
If you’re searching for GHS-approved labels, we have you covered. Discover high-quality GHS labels today.