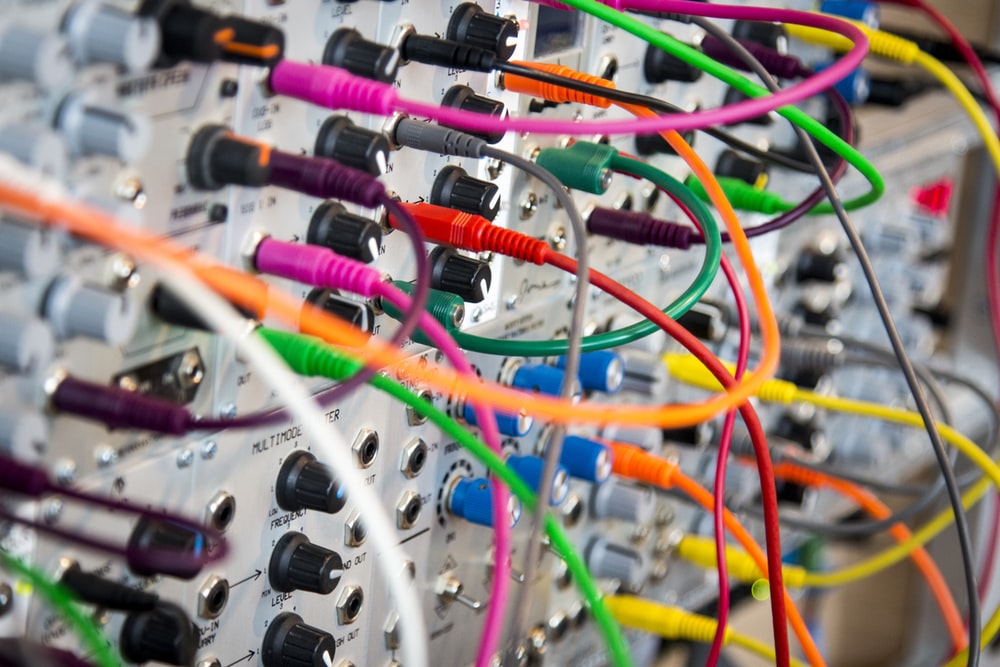
Poor cable management leads to cables that aren’t only annoying to untangle and wrestle against, but are also a serious health and safety risk. Alongside the risk it poses to workplaces, there is a multitude of efficiency reasons as to why a proper cable management system pays dividends.
With half of the UK’s workforce placed in offices, cable management is essential to keep them working efficiently and, most importantly, safely. Plus, let’s face it, looking at tangled-up cables for too long can get anyone on edge!
How Can Cable Management Help Workplace Efficiency?
When you picture the ideal office workspace, what comes to mind? Images of things like a cushty back-supporting chair, plenty of legroom and adequate desk space comes to mind. One thing that doesn’t come to mind is a matrix of tangled cables beneath your feet. Even if these cables aren’t directly in your way, their presence is the antithesis of organised desk space.
If you do subscribe to an “out of sight, out of mind” philosophy when it comes to cable management, what happens when you need to move desks or the times where you need to replace parts of your computer set up? When replacing these or migrating desks, you will be lost in a mess of knots for longer than you need to be, leading to lost working time, damage to parts and, most of all, a lot of frustration.
For some workplaces, regular inspections are needed for cables and equipment. This is where having a tightly-organised cable management system comes into its own. When complemented by cable markers and cable tags, testing and differentiating different cables becomes easier.
Whenever clients walk through your workspace, you want to make a good impression. Having an untidy desk with knotted-up cables and cables doesn’t look the best, particularly if it’s part of a client’s first time meeting you or your business.
How Does Cable Management Save On Costs?
When cables are allowed to pile up or slack behind equipment, they tend to suffer from crushing and sagging. Over a long period of time, this damages the effectiveness of cables, meaning they will eventually need to be replaced.
Additionally, should maintenance be called, organising cables can bite into the time they spend fixing a problem. The longer they take to solve a problem, the more it will cost your business. Should maintenance need to spend 20% of its time finding the right cables and de-tangling knots, this will add up to a significant kitty of wasted cash.
The Health And Safety Risks Of Poorly-Managed Cables
Using incorrect cables, leaving electrical products on and relying on tangled-up cables is a big fire hazard. Daisy-chaining power strips – a practice where you connect one power strip to another – is worryingly a common practice in some workplaces, which is a serious fire hazard.
Instead of setting up proper cable management, this “easier” solution isn’t a solution at all, it just increases the probability of an outlet being overloaded with power, sparking and igniting a fire.
Slips, trips and falls make up 31% of non-fatal injuries at work according to the HSE. Tangled-up cables are rarely stored away properly, with trips over cables making up a significant portion of office-based work injuries. If an employee trips over a cable left out and you, as an employer, haven’t sorted it out, then you will be liable.
Overall, not operating under proper cable identification best practice and utilising a cable management system is the opposite of a safe, well-managed workspace.
Workplace Products Which Help
Organising cables is so easy that it’s a wonder why it isn’t as common as it should be. By utilising a few products, which you can find here at Label Source, it can be made significantly easier.
To safeguard your cables and operate under proper cable management, you can use the following:
- Safety cable wrap labels – Used to show if cables or appliances have been properly tested, complete with a date for when the next test is due.
- Wire markers – Identifies cables with a number or letter-based system.
- Cable identification labels – Marks and identifies labels with a colour-based system. Comes in diameters from 4mm – 16mm.
- Plastic cable tags – Identifies cables with high voltages or currents.
Establish A Cable Management System Today
In essence, a cable management system can improve workplace efficiency by saving on time during inspection and making repairs easier. Time is money, and nobody wants to spend time detangling a mess of cables on the clock.
For those of you reading who are currently drowning under a never-ending flood of cables, then consider the range of cable management products from Label Source.