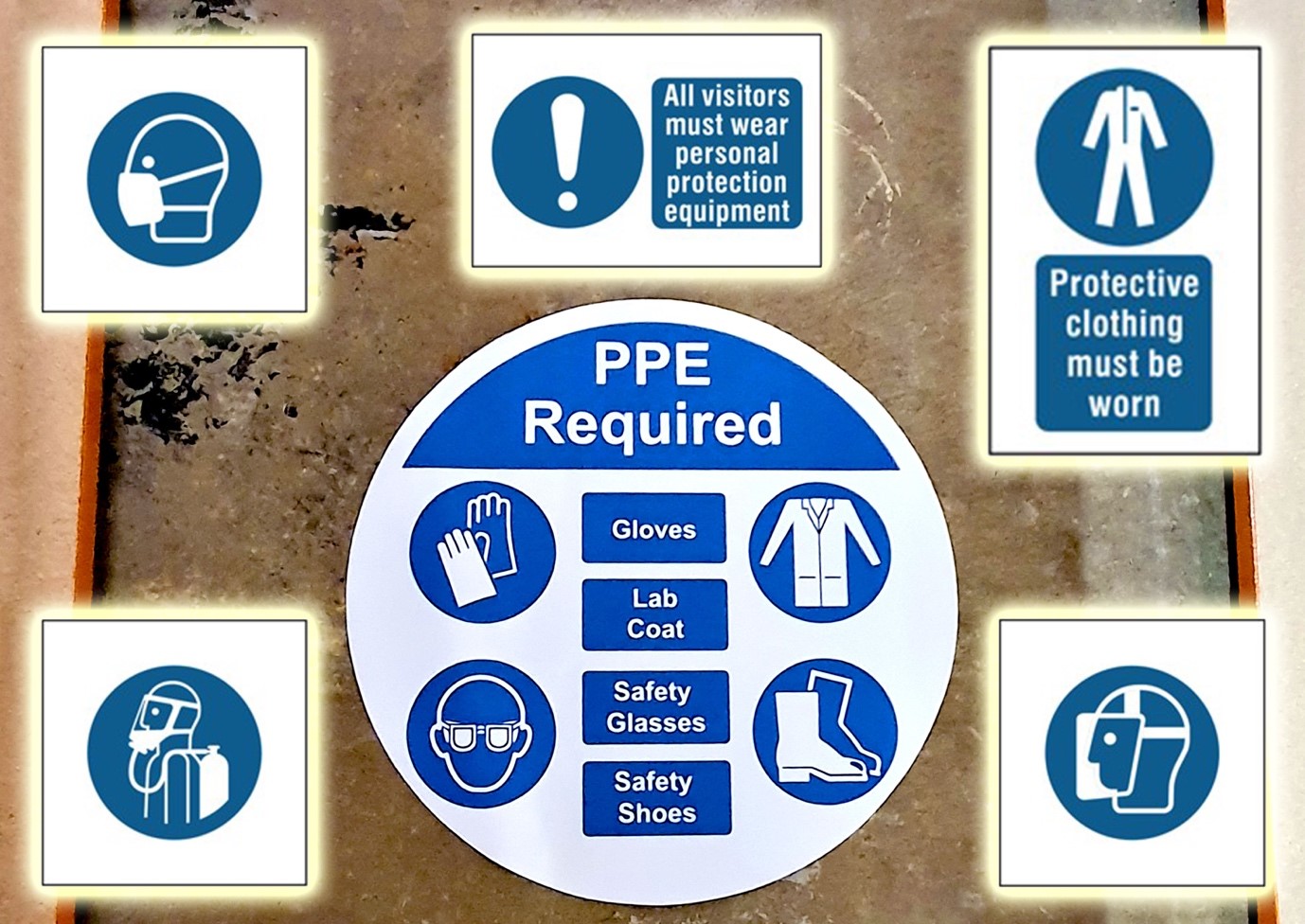
PPE is a hot topic in the UK now. Most coverage has rightfully dealt with the more overt types of PPE such as masks, goggles and gloves. PPE, however, is a broad term, and signs are included under its vast umbrella.
PPE signs and symbols are an oft-forgotten aspect of personal safety in the workplace. They play an essential role in managing protective behaviour by reinforcing safety and keeping staff accountable.
Below, we discuss the place PPE signs have, what mandatory signs certain businesses must have and how they are designed to keep people safe.
What is PPE?
PPE refers to “personal protective equipment”. Broadly, there are eight categories of PPE:
- Respiratory protection – such as ventilators or breathing masks
- Eye protection – such as goggles or spectacles
- Hearing protection – such as ear plugs or earmuffs
- Hand protection – such as gloves or protective cream
- Foot protection – such as specialised boots and shoes
- Head protection – such as helmets or hoods
- Height protection – such as harnesses
- Skin protection – such as long-sleeved or hi-viz clothes and sun creams
From doctors on the frontline protecting themselves from infection to outdoor workers protecting themselves from the sun, PPE is there to keep people safe on multiple levels.
Legally, employers have certain responsibilities when it comes to PPE. Under the Health and Safety at Work Act 1974, employees cannot be charged for the provision of PPE. Under Section 9, the law states:
"No employer shall levy or permit to be levied on any employee of his any charge in respect of anything done or provided in pursuance of any specific requirement of the relevant statutory provisions".
This means, as an employer, it is your legal duty to supply PPE without charge.
How Can PPE Signs Help?
PPE doesn’t end with equipment, however. You need to keep your employees trained in its use and put proactive measures in place to keep them reminded of that training.
This is where PPE signs come in. PPE signs are mandatory signs that are put in place to remind employees to wear what is needed properly.
All of these signs consist of a blue circle with a white background and text panel:
They are easily recognisable, but employers must make an effort for them to be seen by staff and the public (if relevant).
It’s very simple to understand what these mandatory signs mean. They are purposefully and concisely designed to maximise safety and ensure understanding irrelevant of language or cultural barriers.
Perhaps the most recognisable PPE symbols in the UK is the “wear head protection” sign. It’s simple, clear and communicates quickly that headgear needs to be worn.
Fundamentally, PPE signs are there for moments where employees may forget a key stage of their PPE preparation. It’s a much-needed safety net that ultimately saves lives.
Get PPE Signs Today
If you have staff that require PPE, then don’t forget that you need signs, too. Discover our full range of PPE signs today. Be sure to check out our range of social distancing signs, too, to stay safe and accountable.