It was reported that yesterday at a lorry tipped over when traveling along a busy road in wales. As expected the contents of the lorry spilt over the road and caused traffic congestion until pasts 8pm last night.
This lorry was transporting sodium hypochlorite, a chemical which is commonly used as a bleaching agent or in your everyday, household, disinfectant. Sodium hypochlorite is highly dangerous chemical, which omits sodium oxide and chlorine gasses and can cause incredible damage to the environment and humans if ingested or inhaled, due to the nature of this chemical it is classified as a Class 8 corrosive Hazardous chemical.
Luckily no one was hurt in this accident but it did trigger us here at Label Source to think about our own range of Hazardous chemical labels.
Hazard warning labels are there to protect people who are to come into contact with the substance, say if there is an accident the emergency services will know how to respond to the substance to help protect everyone involved and themselves.
When transporting hazardous chemicals you are required to display hazard diamonds on the harmful substances. These hazardous have a different classification and so require different labels.
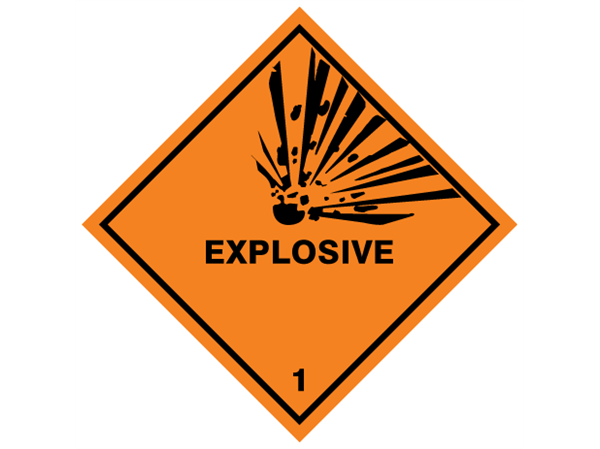
Class 1: Explosive substances and articles, with sub-categories ranging from 1.1 (mass explosion hazard) through to class 1.6 (extremely insensitive substances).
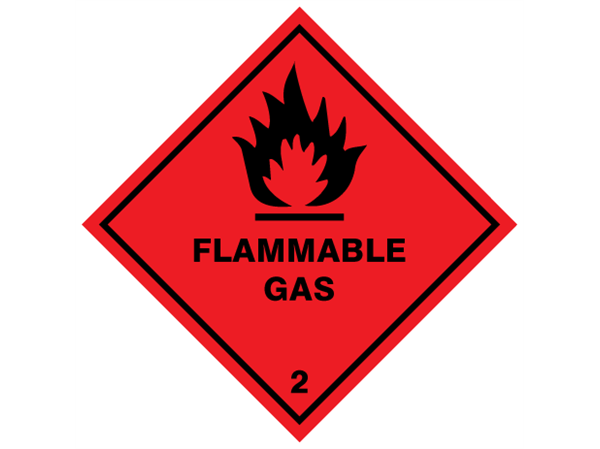
Class 2: Gasses (including compressed gas, liquefied gas, refrigerated liquefied gas, dissolved gas, aerosol dispensers containing gas, and other articles containing gas under pressure and non-pressurised gas).
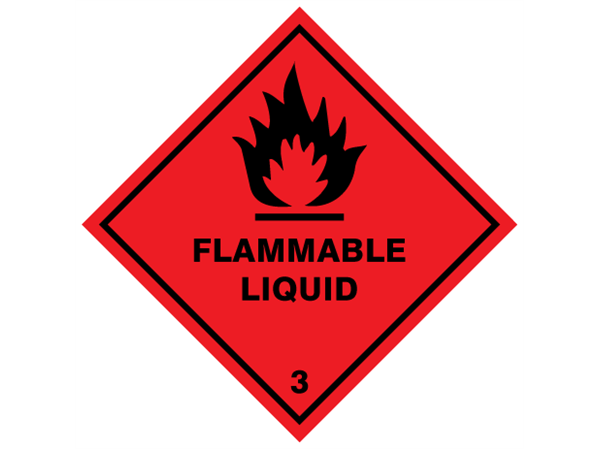
Class 3 : Flammable Liquids
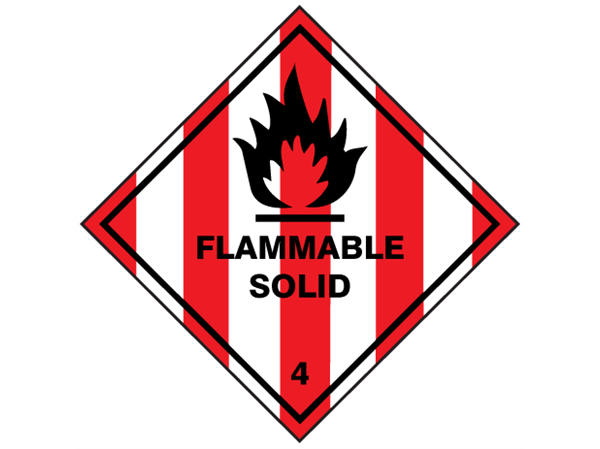
Class 4.1 : Flammable Solids
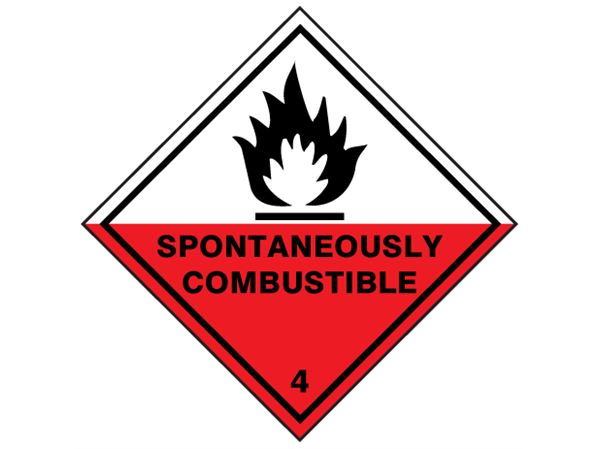
Class 4.2 : Substances liable to spontaneous combustion (including pyrophoric substances, mixtures and solutions - liquid or solid - and self-heating substances)
Class 5.1 - Oxidizing substances, solid or liquid, either self-heating, or emitting flammable gases on contact with water.
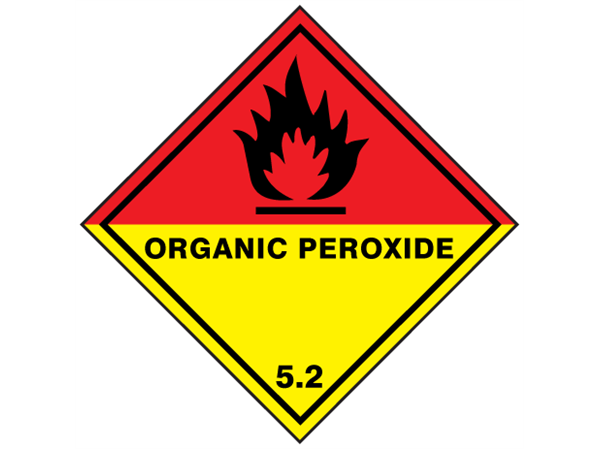
Class 5.2 : Organic peroxides. Substances which decompose at normal or elevated temperatures, or heat up on contact with impurities (acids, amines etc), friction or impact, and release harmful or flammable gases and vapours.
Class 6.1 - Toxic substances that cause damage to human health, or death by inhalation, body absorption or by ingestion.
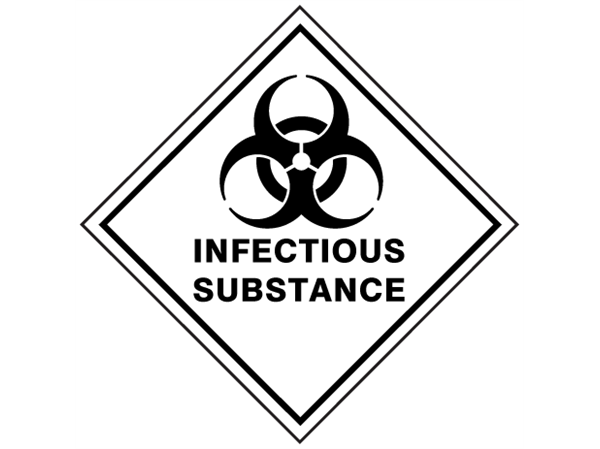
Class 6.2 - Infectious substances that contain pathogens (bacteria’s, viruses, parasites or fungi) leading to disease in humans or animals.
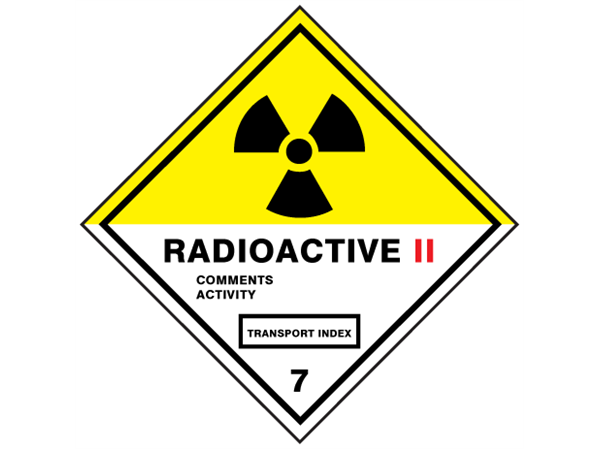
Class 7 - Radioactive material containing radionuclides above permissible levels.
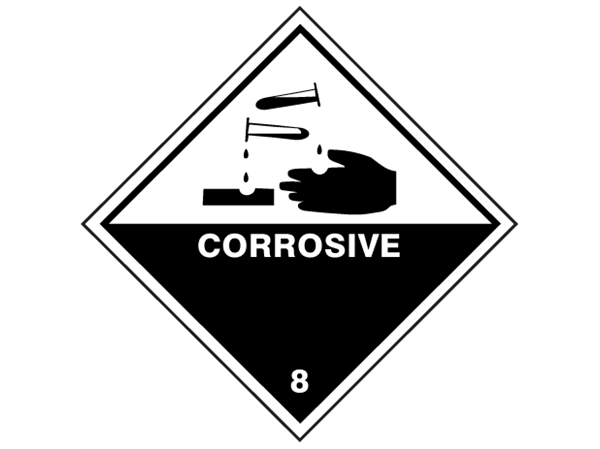
Class 8 - Corrosive substances where skin or mucous membrane is attacked by chemical action, or where goods are damaged or destroyed through leakage
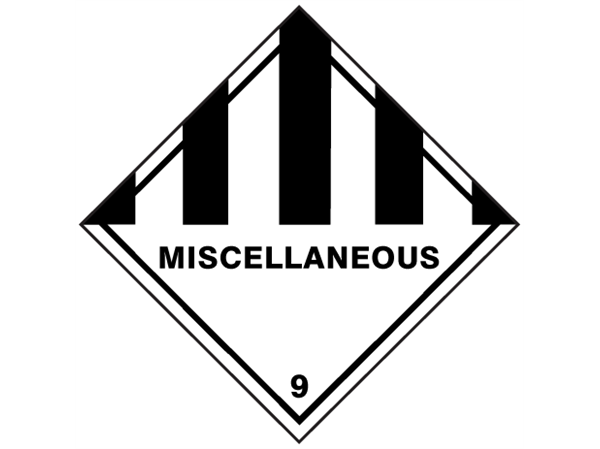
Class 9 - Miscellaneous dangers not covered by the above. This includes: fine dust hazards (asbestos fibres); substances which form dioxins in the event of fire (PCBs); environmentally hazardous materials; substances emitting flammable vapours; lithium batteries; and lifesaving appliances.
Transporting chemicals is a dangerous activity so it is important that you follow the correct safety regulations in case an accident does occur. To ensure that everyone knows about the risk that is involved the hazardous substances have to be labelled on the outside of the carrier, on the substance container and if the substance is in its own packaging on the outside of the packaging, so the hazard is highly visible for all.
You can view our full range of Hazardous Chemical Labels here. If you do have any questions or in the unlikely event that you cannot find the label you are looking for, feel free to contact us by email on info@labelsource.co.uk.