As Michael Crawford is preparing to reprise his much loved character Frank Spencer from the classic BBC television sitcom “Some Mothers do ‘Ave ‘Em” for sports relief, Crawford is famous for performing is own stomach-churning stunts which famously include, clinging onto the back of a bus on roller skates, driving off the end of a pier, sitting in a car hanging over a cliff.
Whilst talking about the reprisal of his character to the Daily Mail, he opened up about the stunts that he cannot perform due to health and safety laws; “I think the one where I am taking my driving test and I drive off the end of the pier into the sea. I don't think they'd allow that now.'
Michael says 'these days it's all much more difficult with health and safety rules. We didn't have those 42 years ago.'
Health and safety laws exist to safeguard people against being seriously or fatally injured at work, or made unwell within their work place. The regulations are in place to help protect people well-being and save lives, not prevent people from having fun.
Health and safety receives a lot of bad press, especially when companies impose “ridiculous” bans in the name of health and safety, for instance, the holiday resort giant, Butlins banned dodgem cars bumping into each other in their Skegness resort, the banning of street parties after the royal wedding, flying kites on a popular beach in Yorkshire and children being banned from playing football at school – unless the ball is made from sponge.
These examples cause uproar in the media, with people exclaiming that “health and safety has gone mad!” and in these instances, yes it has! These are examples of people wrongly citing health and safety as a reason to prevent people from doing relatively harmless activities.
Granted, bumping into people in a dodgem car is not as dangerous as somebody sitting in a car that’s hanging over a cliff. But the media (most of the time) does not portray the importance of health and safety and why some bans are implemented in a positive light.
This bad press that health and safety receives is detrimental to the cause. The now common misguided conception of health and safety has led people away from focusing on the prevention of real workplace risks. Say, for example, your company have been performing a task a certain way for years and regulations come in guiding you on how you can complete the task in a safer manner, or prevent the task from being completed outright, it’s not health and safety gone mad, the regulations are in place to help you maintain high safety standards and protect your workforce.
For more Health and Safety news follow us on Facebook and Twitter!
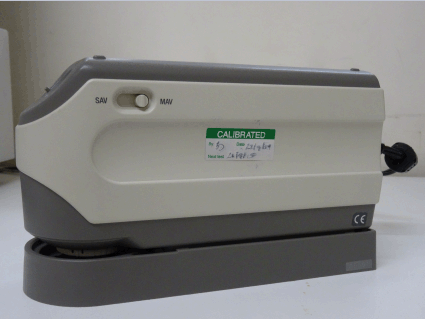
If you are tired of having to periodically replace your labels then our range of Aluminium Foil Labels could be the answer to your problems!
Our Aluminium foil labels have a wide operating temperature range from minus 45 degrees through to 130 degrees Celsius. Where general labels will become burnt and damaged, and unstuck. Aluminium foil labels will maintain their stick and will not lose any detail.
If your labels are commonly exposed to harsh elements, chemicals, or continuous abrasion then your general purpose labels may not be able to withstand the harsh environment leading them to become, illegible and permanently damaged so you will have to replace your labels frequently. Aluminium foil labels are particularly popular with many customers who work in particularly harsh climates because they are extremely long lasting and incredibly durable.
Aluminium foil Labels are perfect if you are looking to implement a new asset management system within your company. Our Specialist aluminium foils feature a permanent adhesive, so when they are attached to your assets they are incredibly difficult to remove, making these perfect for deterring theft, and tracking your fixed and mobile assets.
Many people prefer to use aluminium foil labels because of their flexibility, and versatility. Aluminium foil labels can be fixed to flat or curved surfaces easily and smoothly without air bubbles, or creases in your labels which could contribute to labels becoming damaged, further down the line.
As you can see, there are many benefits to using Aluminium foil labels instead of your general labels. Here at label Source we have a huge variety of Aluminium foil labels ideal for asset marking, quality control, inspection, calibration and more! Click here to view our full range.
If you have any questions about Aluminium labels, or you would like to talk to us about placing a bespoke order, please contact us on 0800 3761 693 or email us on info@labelsource.co.uk.
An environmental management system is a set of processes and practices in place within an organisation to reduce their environmental impacts and increase its operations efficiency.
Having an environmental management system in place in your workplace is an absolute must for any modern day business. Implementation of an environmental management system will not only reduce your businesses carbon footprint, it will also reduce your business costs by wasting fewer resources.
Creating a successful Environmental management system requires the following to be completed by your company:
- Design and develop an environmental policy
- Identify how the company interacts with the environment and plan to make improvements by setting objectives and strategies to meet them
- Implementation of your EMS strategies
- Continuous monitoring of the system to ensure that the goals are being met
- Review of the system and the companies’ environmental performance.
Here at label source we supply a huge range of Environmental Management signs and tapes all compliant with the ISO 14001 regulations.
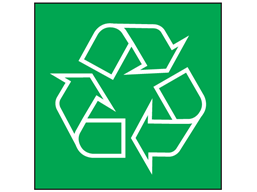
Encourage your employees to recycle their waste in the work place. We supply recycling signs, which feature the instantly recognisable “Mobius loop” recycling symbol clearly printed in white in a green background. These signs cover a wide range of recycling materials such as;
- Glass
- Paper/card
- Metals
- Plastics
- Aluminium and more.
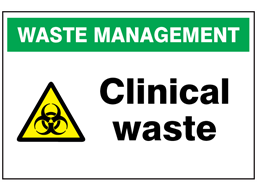
Clearly label your bins for clear waste segregation. In any Environmental Management system, waste segregation is incredibly important. Segregating your waste ensures that it gets disposed of in the correct manner. To help your employees identify and segregate waste within your management system it is best practice to use waste segregation signs. Here at Label Source we supply a range of waste management signs used to identify various different types of waste such as hazardous waste, food waste, recyclable solids and more.
We also supply a range of WRAP recycling signs, Wrap signs are highly visible colour coded signs that encourage the correct disposal or recycling of various materials including Textiles, plastics, electrical, glass and more. Click here to view our full range of WRAP Labels.

Protect the environment and put in steps to conserve energy. Switching off lights, machinery and computers when not in use will not only help reduce the carbon footprint, but will also save your company money. Using our resource conservation signs and notices around your workplace will encourage your employees to take energy saving measures whilst at work. These signs are available for water, electricity and heating conservation and more.
Click here to browse our full range of Environmental Management Signs.
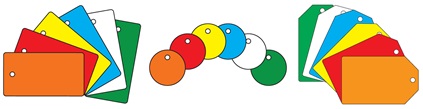
Our plastic tags are robust, versatile, and completely customisable. This means that they are suitable for a huge variety of different requirements - here are a few examples of how they can be used:
- Quality assurance. Goods can be tagged as 'passed', 'failed', 'awaiting inspection', or any other status as required - simply customise the tags as needed. Since our plastic tags are available in six different colours, you can also implement a colour-coding system, e.g. green for 'passed' and red for 'failed'.
- Inventory and stock taking. Again, the various colours that we supply allow you to organise your goods/equipment into a user-friendly colour-coded system.
- Servicing. Tagging/labelling is an important part of servicing and maintenance, and our blank plastic tags allow you to designate your own labels to suit your requirements.
Our Plastic Tags at a Glance
- Can be used indoors or outdoors
- Supplied in packs of 500
- Made of 0.5mm thick polypropylene
- Melting point: 160 degrees Celsius
- Available in six different colours: red, orange, green, white, blue, yellow
- Various shapes and sizes available
As mentioned above, our plastic tags are fully customisable, and their durability allows them to be used in practically any environment. Click here to order your plastic tags, or contact us now if you have any questions.
The purpose of road safety signs is to prevent accidents by providing clear instrustions for drivers and pedestrians to follow, but sadly, the clarity and prominance of the sign does not always lead to the intended outcome. As you will see from our own safety signs, the desired message is always displayed in simple, easy-to-read format, usually using bold prominent colours to attract the attention of the viewer. Sadly, all this effort is irrelevant when people choose to ignore the signs of their own accord, or attempt to challenge the validity of the sign when they are not a safety professional themselves.
While many would say that this is an aspect of safety that is simply beyond our control, a new system in Oxfordshire could soon prove that it is possible to influence the behaviour of careless drivers with the use of safety signs alone. These signs, however, have one distinct difference from your average warning or road safety sign - they have an inbuilt CCTV system! Just as shop owners display signs that warn of CCTV in operation in an attempt to deter shoplifters, these signs were created in the hope that the presence of video evidence would deter drivers from actively ignoring the signs or attempting reckless behaviour.
Oxfordshire County Council launched this scheme with construction company Skanska, after a series of road rage incidents and injuries during the 18 months prior to its introduction. It was found that workers were being verbally abused while carrying out work, as well as being put in immediate danger of being fatally injured by cars who ignored the signs. Thanks to the new wide-angle automatic recording systems installed in the signs, they will be able to monitor and capture any dangerous or abusive actions, which will not be tolerated.
While the system is currently opereating in specific areas only, it would be interesting to see what impact such a scheme could have, if put into practice across the UK. Could this be the future of road safety signs, or even safety signs in general? Is it possible that the only way to impact an individual's response, is to make them aware that you are monitoring it?
Let us know what you think about this idea on Twitter and Facebook.