Health and safety executive have released a new strategy for the health and safety systems that will take us through to 2020, this strategy have been broken down into 6 key themes. In order for this to be successful it requires us all to work together, communicate about health and safety changes in the workplace, everyone taking responsibility for health and safety, employees as well as employers, share new ideas about how to combat challenging health and safety risks, helping businesses grow by simplifying risk management and tackling the costs of work related illnesses head on.
2004/05 Health statistics
- 545,000 cases of ill health
- 223 people were killed at work
- £17.4 billion estimated cost of injuries and ill health from working conditions
- 35.2 million working days lost
2014/2015 health statistics
- 1.2million working people are suffering from a work-related illness
- 2,538 people died from mesothelioma due to asbestos exposure (2013)
- 142 people were killed at work
- 76,000 people reported injuries under RIDDOR
- 611,000 injuries occurred at work
- 27.3 million Working days were lost due to work related illness and work place injury
- £14.3 billion estimated cost of injuries and ill health from current working conditions. (2013/14)
Stats from HSE
Over the last 10 years we have all been working hard to create a safe working environment for our workers and our efforts are paying off! Here in GB we take health and safety extremely seriously and our Health and Safety Record reflects our efforts. Currently GB’s Health and Safety record is one of the best in the world. However, this doesn’t mean that there isn’t room for improvement.
Here, at label Source we have put our heads together and come up with 5 tips on how you can improve your workplace safety in 2016:
Plan to control workplace hazards
Identify all the hazards in your workplace and make sure you take the relevant steps to completely eliminate the hazard, or at least minimize them. To do this you will need to develop a comprehensive safety plan.
Make sure that if you cannot completely eliminate a workplace hazard, that you are alerting people of the hazard through the use of safety signs.
Train your staff
Comprehensive training must be given to all members of staff, especially if they are expected to work in an environment where there is a risk of injury. Make sure that you provide all of your employees with a written document outlining all the companies’ safety procedures so they have a point of reference. If you are not training your staff to a high level, you are endangering your employees. If your company is found to be guilty of health and safety breaches, your company will be held liable if there is an incident and could lead to your company having to go to court.
Inspect your workplace, frequently
Make sure that any machinery, tools, equipment that your employees are using are well looked after and maintained on a regular basis. Across the UK thousands of accidents happen whilst people are operating machinery. This could be because they are not wearing the correct PPE, the machine is malfunctioning and no one has reported it or the workers are simply not trained to operate the equipment.
You can help prevent injuries to your staff while they are operating dangerous machines, using hazardous tools & equipment or whilst they are working in a hazardous area by using mandatory safety signs. These signs serve to remind your workers of what is expected of them, for example, wearing the correct PPE, using the correct equipment through to washing their hands – to prevent the spread of disease.
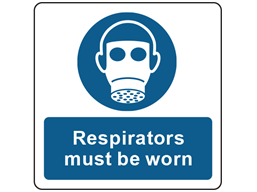
Investigate all incidents
Not all incidents are fatal, not all incidents cause injury or illness, however it is important that if there is an incident that it is investigated to determine why the incident happened and what can be done to prevent the hazard getting worse and happening again.
Keep up to date records
Ensure that you are keeping a record of all the incidents that occur, all the accidents that happen, first aid treatment, inspections, and training. By keeping up to date records you will be able to identify any tends in incidents. Maybe there is a gap in their training – keeping records will help you identify this.
Join in the conversation at #HelpGBWorkWell
Follow us on facebook and twitter for regular health and safety blog updates.