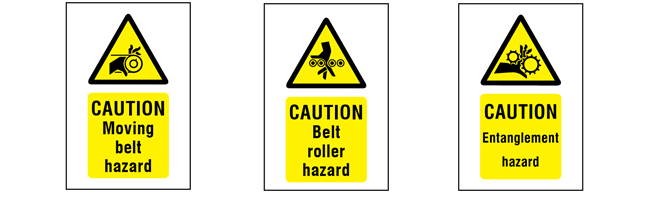
A textile company based in Devon has been fined after a workers hand was crushed. The incident occurred at the Heathcoat Fabrics Ltd factory after the worker was preparing a piece of machinery for the next shift, when his hand was drawn into rotating rollers. He suffered severe crushed hand injuries which resulted in the amputation of 4 of his fingers.
An investigation by the Health and Safety Executive (HSE) found that Heathcoat Fabrics Ltd had failed to safeguard the machine, making it very dangerous to use. A guard was previously fitted to the machine, but when it broke down;the company had failed to repair it, and instead replaced it with an emergency stop wire. The machine was left un-guarded for over two years, and a guard wasn't fitted till after the incident occurred on the 23rd August 2014.
The company pleaded guilty to breaching regulation 11 of the Provision and Use of Work Equipment Regulations 1998, and were fined £300,000 and ordered to pay costs of £2862.30.
To prevent a similar incident occurring at your workplace, it's important you ensure that every safety measure has been put in place to ensure your workers remain safe when using machinery that posseses a risk of entanglement. Here at Label Source we have a wide choice of entanglement warning signs that will inform your workers of the risks of using that machine, and to take extra caution, preventing any incidents or accidents from happening. To view our range of entanglement warning signs, please click here.
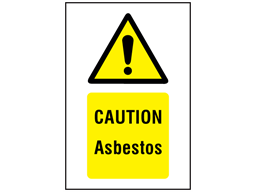
An Argos store in Plymouth has reopened after health and safety chiefs shut it down following the discovery of asbestos. The Argos store, as well as a construction site next-door were both closed suddenly after the Health and Safety Executive discovered the asbestos. The construction site - a former Derry's department store, which is currently being converted into student flats - was where the asbestos was found, and Argos was closed as a safety precaution.
The Argos store was closed for a week, and work had stopped on the construction site as a precaution in case there were any airborne asbestos fibres. After extensive monitoring, all areas of the site was cleared and wok recommenced on Monday (20th February), and the Argos store re-opened the next day (Tuesday).
Asbestos is a natural fibrous rock that was widely used within buildings until 1999. It was widely used from the 1950s to the mid-1980s, due to it being a good insulator and having good fire protection properties. You will find asbestos in buildings built before the year 2000. Asbestos materials present a risk to your health when the fibres become airborne. This will happen if you cut, drill or break materials containing asbestos. It's the biggest occupational disease risk to construction workers; and therefore, safety precautions need to be put in place.
Safety signs and labels need to be put in place to warn workers of the presence of asbestos and that suitable safety precautions are made. Here at Label Source we stock an excellent range of Asbestos Safety Warning Labels and Signs to ensure your workers are aware of the substance, reducing the risk to their health and safety. If you wish to view our range of Asbestos safety labels and signs please click here.
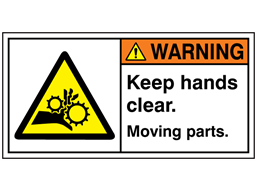
A week has gone by, and we have yet another story to bring to you of a firm being fined for poor safety procedures. It has been reported by WirralGlobe that Cammell Laird have been fined £400,000 for safety failings, after a worker suffered serious injuries whilst carrying out repair work at the Birkenhead shipyard. The 59-year-old from Ellesmere Port, Cheshire, sustained fractures and crush injuries to his right hand in the incident on July 20 last year, and the accident had made him unable work for 5 months, but has now returned.
The incident was investigated by the Health and Safet Executive (HSE) which prosecuted Cammell Laird Shiprepairers and Shipbuilders for serious safety failings. Liverpool Magistrates Court heard this week that the worker was repairing a lathe at the time of the incident. Whilst completing the repair he noticed that the shafts and couplings were dirty. In order to clean these components, he wrapped emery cloth around the lead screw and switched the lathe on. As the machine run, his right hand was pulled in to the moving parts, resulting in his hand being crushed.
A system of lock off, which would of prevented reconnection of the power to the machine, had been identified and was outlined in the written health and safety management system; however, it had not been properly communicated to employees or implemented. Cammell Laird pleaded guilty to breaching section 2(1) of the Health and Safety Work Act 1974 and were fined £400,000, and ordered to pay costs of £7,683.
Health and Safety should be a concern for any organisation. It is the responsibility of the business owner to ensure to carry out a thorough risk assessment and to ensure that all measures possible have been taken to minimise the risk of someone coming to harm at your workplace or as the result of your operations.
To ensure that a similar incident like this one doesn't happen to you, we stock a fantastic selection of Safety Lockout Labels & Signs, as well as a range of Moving Parts Warning Signs.
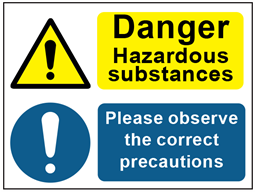
PP Construction Safety has reported that Martin Baker Aircraft Company Ltd - an ejector seat manufacturer - have been fined £800,000 after three workers developed debilitating lung conditions. The three engineering operators developed extrinsic allergic alveolitis after being exposed to the mist of working metal fluid for a large number of years. The lung condition, also known as hypersensitivity pneumonitis, is the body's allergic reaction to breathing in a substance and symptoms include coughing, shortness of breath and joint pain.
The workers had served for the company for more than 20 years, and were exposed to the working metal fluid mist for at least three years. The fluid is used as a lubricant and coolant in engineering processes. During these processes the fluid creates a mist, which in this particular case it has been inhaled by roughly 60 workers. One of the workers has been seriously affected by this incident, and he is now virtually paralysed by this illness. Another will never be able to work with the fluid again - a key material in the engineering industry. And the final worker must have measures in place to ensure he never comes into contact with the substance again.
HSE investigators found that the measures in place within the factory to control the exposure of the mist were inadequate. The company had failed to put in place a system of clearing away the excess fluid or providing extraction to prevent the build-up of the mist. There were also failings in the provision of health surveillance, which should have identified the issue early enough to ensure the company were able to put in place and monitor any appropriate safety measures.
The company have pleaded guilty and were fined £800,000 and ordered to pay costs of up to £36,912.36.
To ensure a similar incident doesn't happen to your company, ensure that there are suitable COSHH Signs have been put in place. To view our range of COSHH labels, click here.
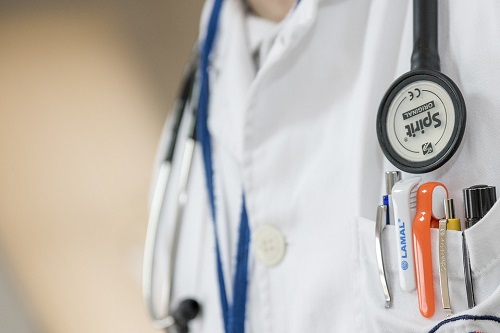
In the last couple of days a new Press Ganey report has come to light; that highlights the impact of nurses' perceptions of workplace safety and their ability to assess and a accurately treat patients. The main focus of the report was the nurses' perception of workplace safety and their ability to monitor, evaluate and act on their patient's change in health. Nursing practice is vitally important to ensure that a high-quality and empathic care is provided for both patients and caregivers. Christy Dempsey, chief nursing officer at Press Ganey pointed out that integrating workplace safety and surveillance programs throughout the healthcare facility improves outcome measures, whilst also encouraging a commitment to nursing excellence.
The report noted that for healthcare facilities where nurses experienced high workplace safety:
- A 52% lower rate of missed care, as perceived by nurses.
- 27% of nurses at these facilities expressed greater job satisfaction.
- A 22% higher CMS Overall Hospital Quality Star Rating
- There was also 26% decrease in hospital-acquired pressure alcers (also known as bedsores) at facilities where nurses felt that they were able to respond quicker to their patients' changing status.
These stats are very promising, and they back up Christy's point that workplace safety and surveillance programs helps improve outcomes in healthcare facilities. To help improve nurse safety, the report recommends organizations to:
- Carry out adequate unit staffing that takes into account patient volume, nurse-skill mix and the intensity of care each patient requires.
- Ensure that uninterrupted, and sufficient meal and rest breaks are taken.
- Use patient data to improve scheduling and decrease extended work shifts.
- Develop a stable core of nurse leaders and nurses with leadership potential through taining and/or formal programs to develop these skills.
- Hire and retain a high percentage of RNs with a bachelor's degree or higher, and nursing specialty certifications.
If your organization meets these guidelines then they're certainly going to see an increase in nursing excellence, which will in part, improve nurse and patient outcomes.
For more H&S news and insight, be sure to follow Label Source on Twitter.