Quality control measures are a hugely important measure for ensuring public safety, particularly in production line environments. Implemented by a standardised system of inspection and testing, these procedures allow products, components and assemblies to be monitored and assessed, according to the recommended safety and quality standards of each particular industry. This prevents potential hazards to the workforce and public, while also helping to ensure that the set quality requirements are being upheld.
To track and implement this system efficiently, companies often use visual indicators to communicate the status of each item, and to keep track of scheduled inspections. Here at Label Source, we stock a huge selection of quality control and calibration labels, which are designed for the purpose of clearly indicating the test status of the item in question. One of the most important label types in this selection, are our 'QC Rejected Labels', which are used to indicate failed inspections, and provide appropriate warnings. By using these labels to highlight testing and monitoring failures, employees are able to take the correct action in response to this status, guarding their own safety, as well as that of the public.
Here are some of the QC rejected labels that we provide:
Rejected Label w. Date & ID
This QC rejected label not only provides a striking visual warning about the item in question, but also provides evidence of inspection, with space to add personal details and the testing date.
Jumbo Quality Assurance Labels
If you have a larger item or piece of equipment that needs to be marked, these jumbo labels are the ideal way to provide clear visual notices on a larger scale.
Rejected Label With Remarks
For enhanced details, we also provide QC rejected labels with space for additional comments. This allows the reason for failure to be explained, and can also be provided as a guide for further action.
To see our full selection of quality control labels, click here!
It is sometimes difficult to quantify the cost of poor quality. Customer complaints, returned goods, lower productivity through re-working or new manufacture, and waste materials are just some of the elements to be considered.
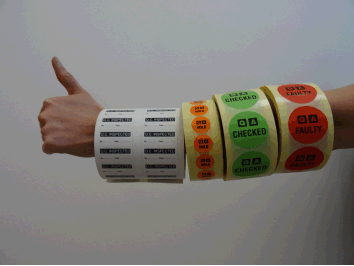
Thus, QC inspection forms a vital function in detecting and preventing defects, in both products and processes, to provide corrective actions and for preventing defective goods being shipped to customers.
Not only does this fortify bottom line financial performance, but has a critical impact on; reduction of waste, scrap or pollution; lower maintenance costs; increase productivity and operator efficiency; and bolster staff motivation and morale.
Label Source supply a range of QC and QA labelling for marking products, and in identifying their quality status. These include our QC inspection ranges, Inspection labels and our Production status label ranges.