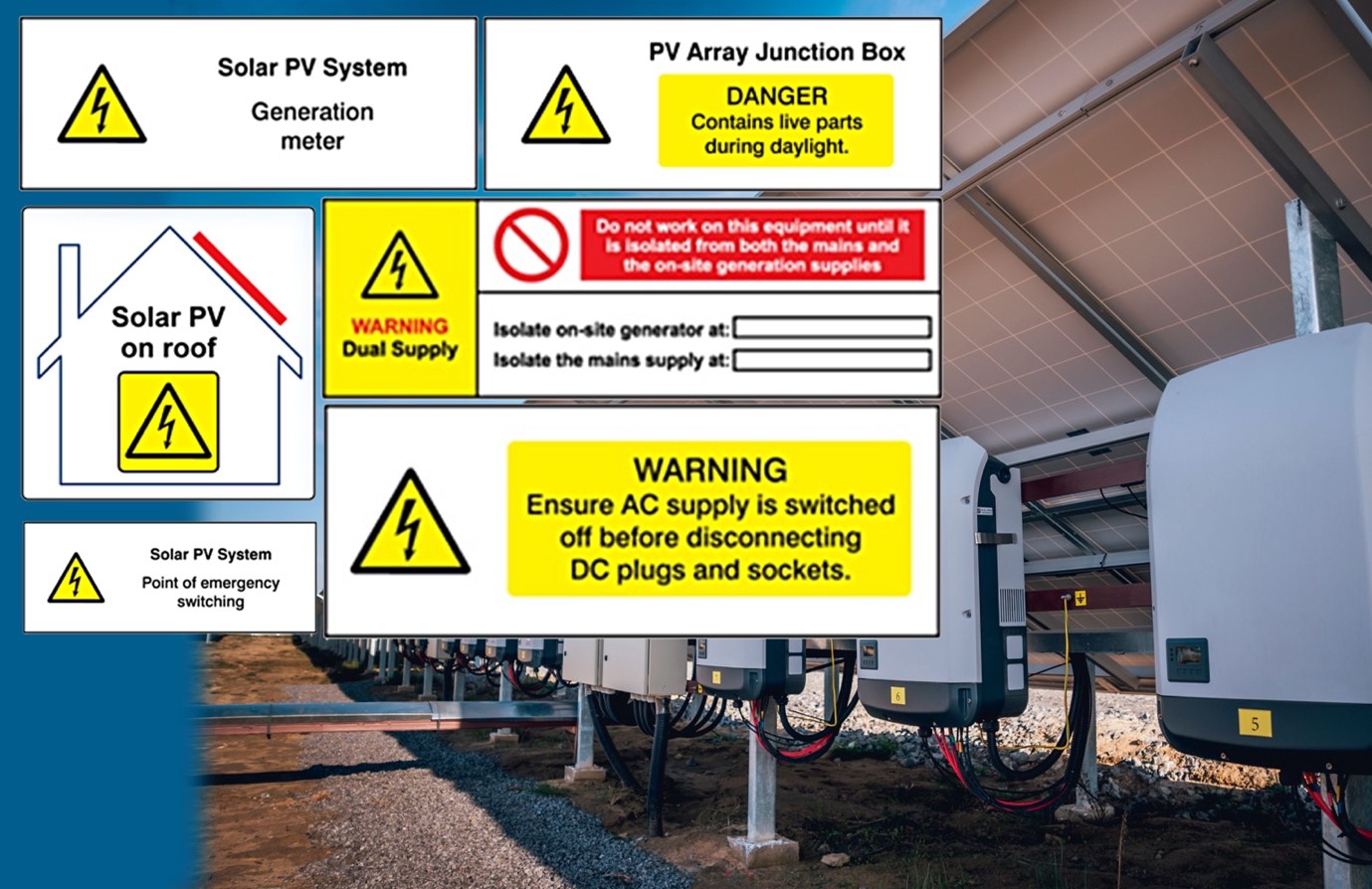
Solar energy is, thankfully, rising in popularity. Once thought of as something too expensive for the regular consumer, solar panels are now regularly seen on modern builds, older homes and office buildings too.
According to industry predictions, solar energy is set to be worth $176.2 Billion by 2027. Of course, whenever an industry explodes in popularity, safety measures must be reviewed. If you’re thinking of installing solar panels, then you need to know all about solar panel safety.
Below, we discuss what a photovoltaic cell is, its role in solar panel installation safety and some general solar guidelines. More...
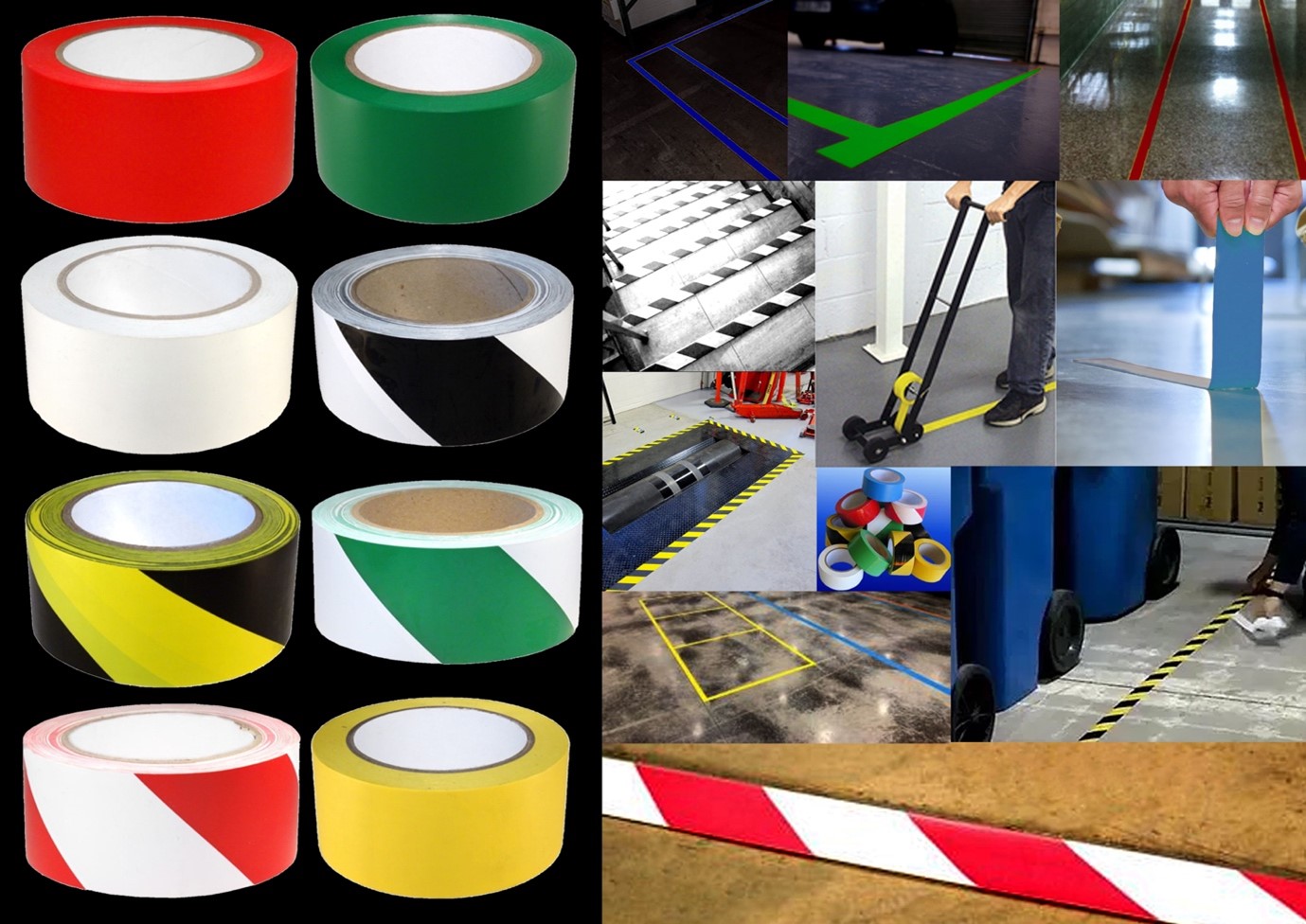
Floor tapes are used in many workplaces, from warehouses and factories to shops and offices. They’re a versatile, multi-purpose tool that promotes safety, streamlines processes and improves workplace efficiency.
Below, we discuss how to install floor tapes, the different uses of floor marking tapes and why they’re important. More...
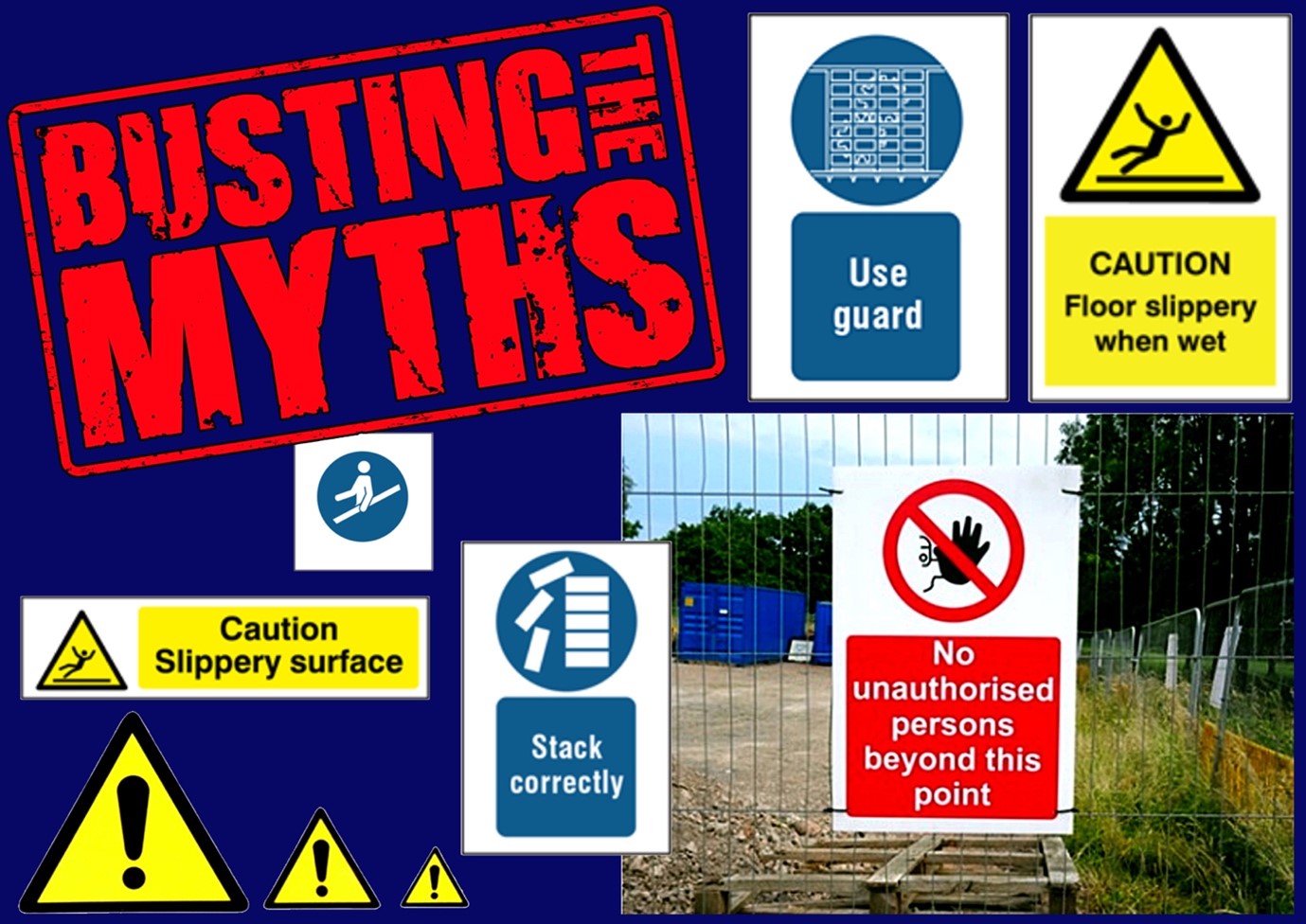
The Health and Safety at Work Act applies to everyone who works in the United Kingdom. You can work a desk job, as a firefighter or in a customer service role – it doesn’t matter, this piece of legislation will apply to you.
Even though the Act was written in 1974, it still maps out modern employer and employee responsibilities, even with the changing tides of technology and employment.
So, as an employer, you need to know the Health and Safety at Work Act policy inside-out. Below, we put your health and safety knowledge to the test. More...
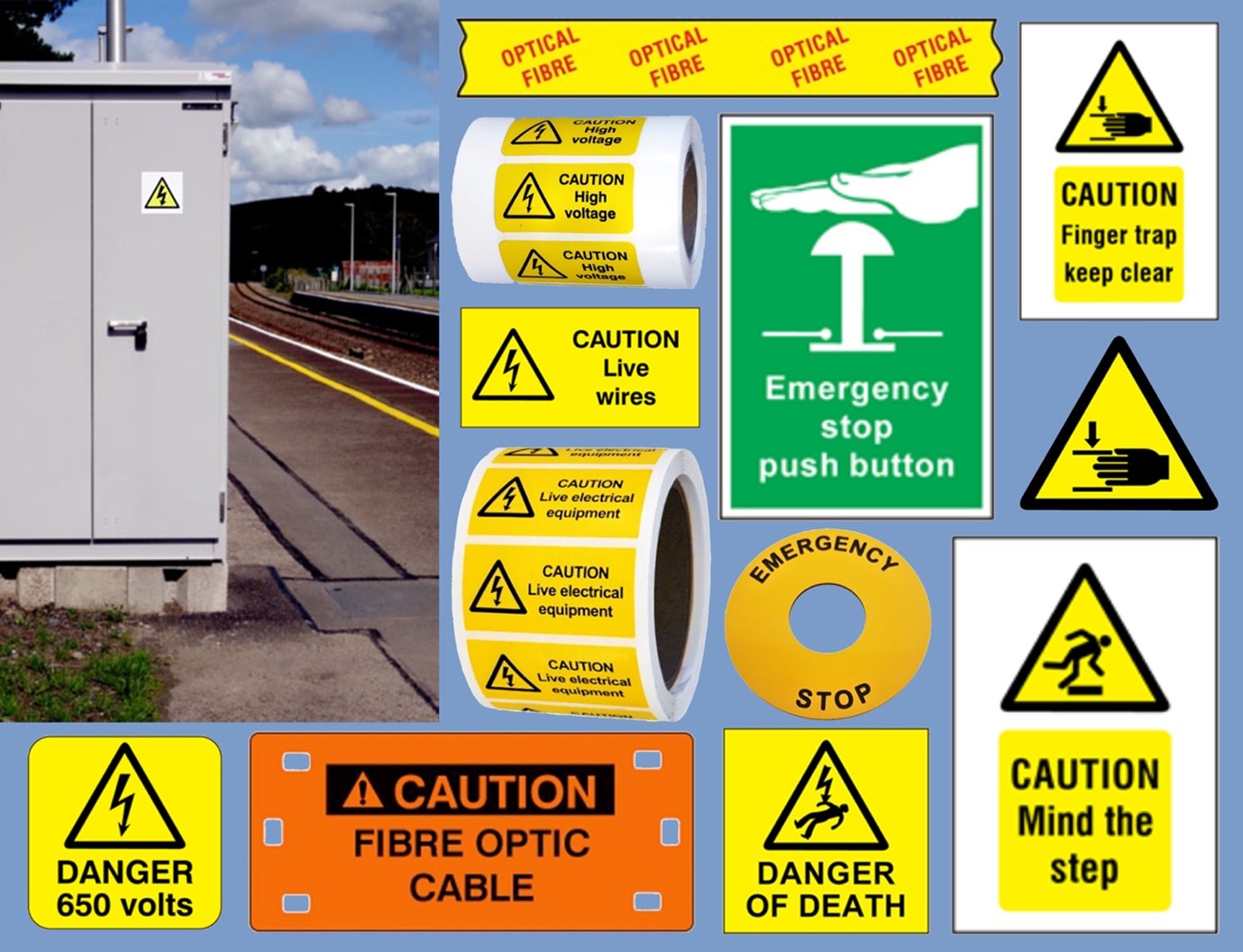
Britain is a country built on its railway networks. From transport to exports, railways are a major source of trade, business, jobs and tourism within the United Kingdom.
The importance of railways means there is a wealth of rail-specific legislation and health and safety powers. It goes without saying that railways are dangerous, so you need to know the specific laws in place.
Below, we discuss railway health and safety regulations, including the role of hazard labels and railway guidance. More...
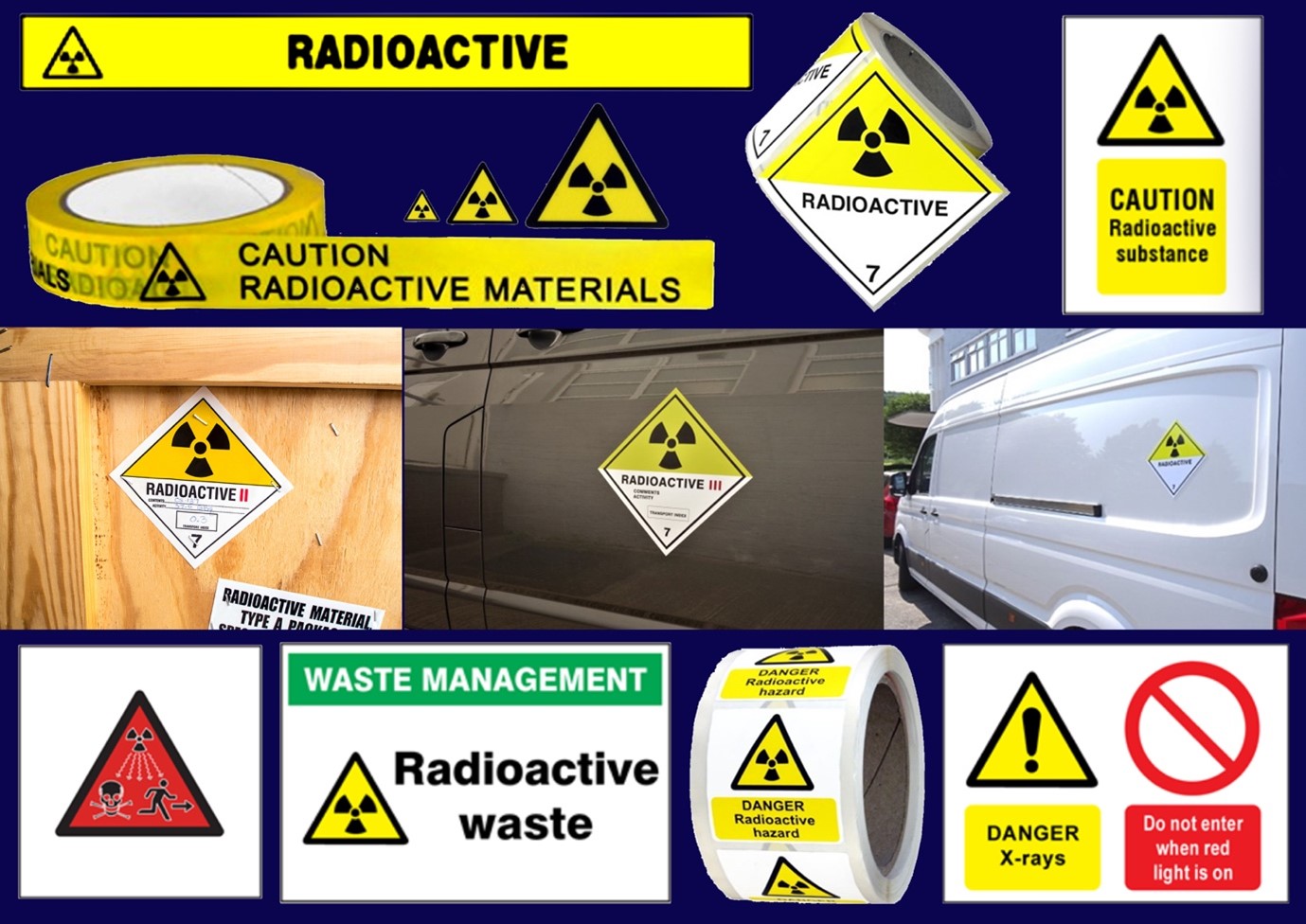
As many of you know, radiation is no joke. You need to stay incredibly safe around radioactive material, and radiation safety procedures are extremely stringent.
Underpinning these detailed safety procedures is a system that relies on radiation labels; if people aren’t aware of radioactive material, then they can’t protect themselves against it.
Below, we discuss how radiation labels are integral to radiation safety, the importance of radiation risk assessments and other safety procedures. More...