
As the pressure continues to redevelop brownfield sites, there is the need to dismantle defunct buildings, and provide site clearance. A paramount consideration during any demolition or structural alteration of buildings is that it is conducted safely and in a controlled manner for members of staff, sub-contractors and the general public.
Hazards can be numerous and varied, and these can include;
Falling from heights. This can include falling off the edge of building structures, through openings or off partly removed floors. Risk assessments need to be made for safe access, control of work on fragile surfaces and safe use of ladders and scaffolding structures.
Falling objects. Injuries sustained from being hit by parts of the building structure or from tools or other equipment. Exclusion areas and hard hat use, together with covered walkways and reinforced cabs on machines, and use of high reach equipment should form part of any safety plan.
Collapsed structures. Injuries from crush, lacerations and entrapment. Weight loadings, age of premises, former use of premises and surrounding structures should form part of any safety assessment.
Risks from connected services. Gas, electricity and telecommunications supply needs to be isolated or disconnected to prevent accidents. If this is not possible then any pipes or cables should be clearly identified by labelling.
Noise and vibration. Dangers exist to hearing from noise generated during demolition, and power tools need to be assessed to prevent hand vibration injuries. Suitable ear protection should be made available, and all hand held power tools (electric, pneumatic or hydraulic) need to be assessed for exposure levels established.
Hazardous materials. During removal workers can come into contact with asbestos, flammable liquids, paints and acids (covered by COSHH regulations), dust hazards, and microbiological hazards (particularly for hospitals etc.). Identification of all site hazards, and supply of protective equipment to handle such dangerous substances.
Risks from outbreak of fire. Where sparks, heat or flames are generated during demolition there is the potential for fire. A fire plan should be regularly updated identifying escape routes, location of fire fighting equipment and fire action training.
Risks from traffic accidents. Plant mobile equipment and vehicles used to remove debris from the site. A traffic plan should be established with designated pedestrian and vehicular routes, clearly marked crossing points, with controlled access for vehicles and establishing turning areas.
Risks from rodents and insects. Potential bites, stings and inhalation of contaminated dust from urine and faeces. It is necessary to provide protective clothing (ie gloves, dust masks), and have a policy on disposal of carcases.
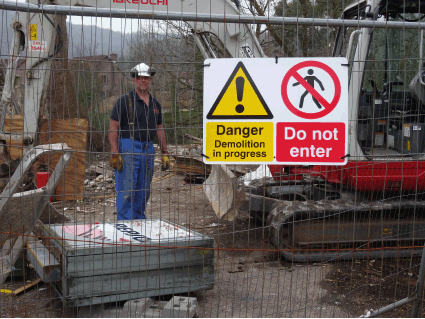
Label Source can assist you with safety induction of staff and subcontractors with our range of health and safety signs to the latest legislation to identify workplace hazards, mark prescribed pedestrian and vehicle routes, fire equipment and access routes, and to identify the mandatory use of protective equipment and workwear. Also, we supply a range of construction related barrier tapes and underground utility pipe and cable marking tapes.